Decades ago, if you asked about coating on a press sheet, the immediate thought was varnishes. Or perhaps, some may have even thought of it in reference to the coating OF the sheet itself, such as gloss, dull, matte or silk. Or perhaps they may have thought of post press coating, such as UV or even lamination. Aqueous coating was applied to the graphic arts field in the 1970′s, and exploded in the 80′s. During the 90′s, while we watched “Friends” debut, or the last few episodes of “Star Trek: The Next Generation”, coating took off, and press manufacturers met the demand with 4, 5, 6 and 8-color presses that had the additional tower for the coating, and the extended delivery for the UV curing.
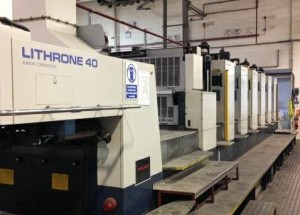
A 6-color 40″ press with an aqueous tower and extended delivery.
WHAT IS AQUEOUS COATING?
Unlike the name suggests, aqueous coating is NOT water-based, but a liquid polymer that dries and cures quickly under UV light. The benefits of aqueous coating are numerous:
- Dries quickly, allowing for work and turn or sheetwise back-ups within minutes, not hours.
- Seals the sheet and protects it, which is vital with certain PMS colors or reflex blue, which can haze as they are trimmed (hazing is NOT offsetting. Hazing is where the the color is transferred at the trim edges from one sheet to the next due to the knife-blade slicing through the paper).
- Does not gas-ghost as varnishes do, and therefore, does not require dry time.
- Will not yellow as it ages, as varnish does.
As aqueous coatings have become more sophisticated, you can find not only gloss, but matte, satin, specially formulated coatings for synthetic papers and for work & turn applications, a high-gloss coating, and a special coating for jobs that will film laminate. Finally, soft touch aqueous is becoming a sought-after type of coating. It has a very smooth surface, but it has a slight texture to it, almost like touching leather. Another benefit of aqueous coating is that it requires no plates as varnishes do, and it has little clean up, so the costs to add aqueous are minimal.
THEN WHY USE VARNISHES?
Varnishes still have their value as design elements, whereas in the past they were used to seal the sheet. For example, doing a spot dull varnish over a solid color with a spot gloss varnish as a design element can have a dramatic impact. Varnishes can be run “inline”, which means they are printed with the rest of the 4-color on that side of the sheet. But varnishes look best if they are run as “dry trap” or offline, meaning run as a 2nd pass on the side of a sheet. Finally, in order to insure that the varnish looks the same from one side of the sheet to the next, the pressmen will run it back through the press to “polish” it.
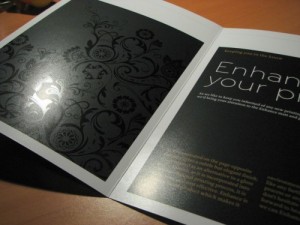
Image from printingwiki.org
WAIT. CAN I DO BOTH???
YES! in fact, a very dramatic effect is what is known as “strike-through” varnish, which again is best used with solid colors. The job is printed with a satin aqueous, then a dry-trap spot gloss varnish is applied over the top of that. This has the same effect as doing a spot gloss and spot dull varnish, but without the cost of 2 additional varnish passes, plates and wash ups. Another effect is using a dry trap spot gloss varnish over the soft touch aqueous, which heightens the effect of the leathery feel of the aqueous. As always, check with your print services provider on what they provide in the way of coatings, and how to prepare your files for these spectacular ways of finishing your press sheet.
No comments:
Post a Comment